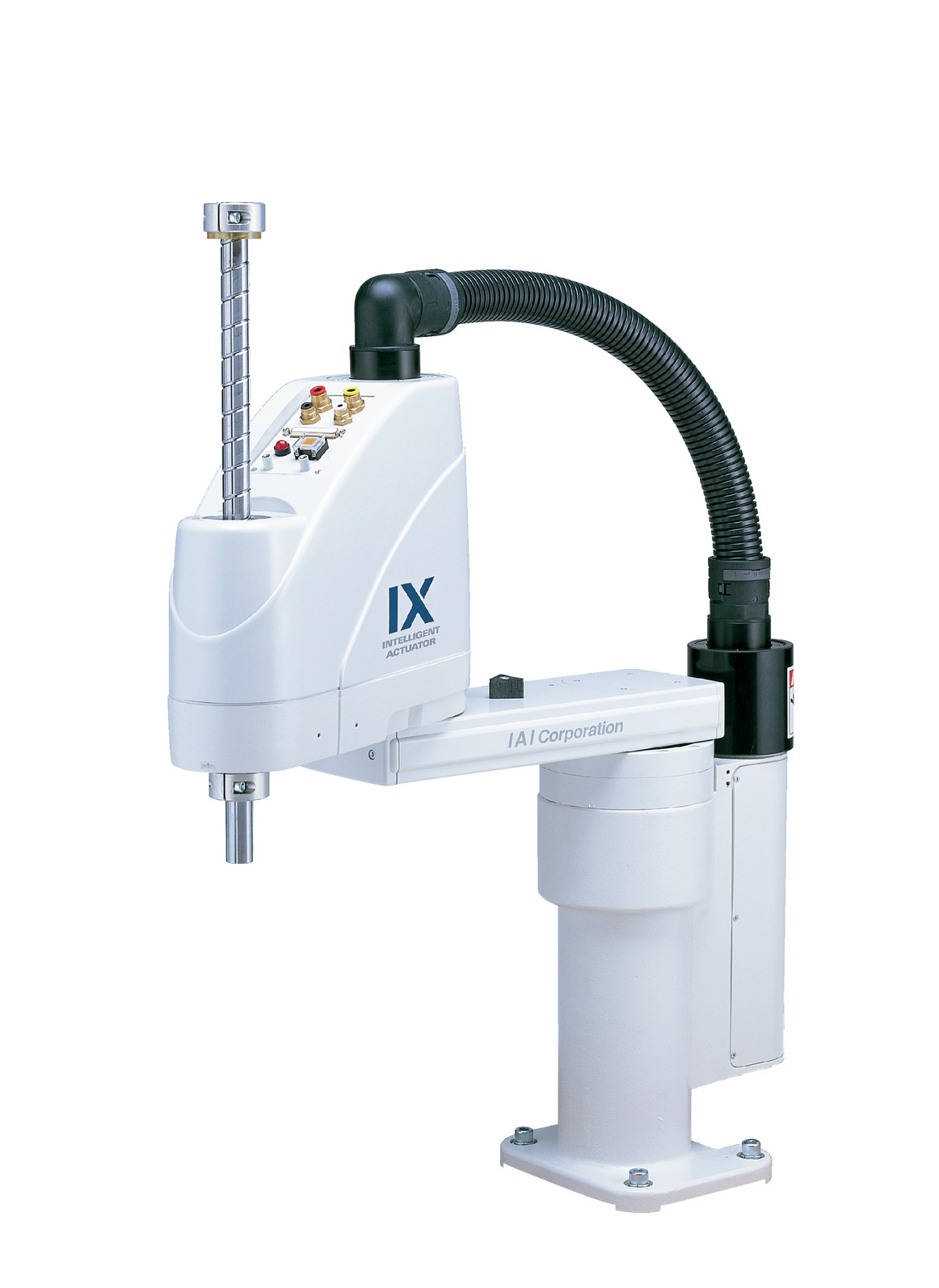
Model specification
Model | Axis Configuration | Arm length (mm) | Motor capacity (W) | Operating range | Positioning repeatability (mm) (Note 1) | Max. PTP operation speed (Note 2) | Standard cycle time (s) (Note 3) | Load capacity (kg) (Note 4) | Control range of 3rd axis (vertical axis) push force (N) | Allowable load of 4th axis | ||||
---|---|---|---|---|---|---|---|---|---|---|---|---|---|---|
Rated | Maximum | Upper limit (Note 5) | Lower limit (Note 5) | Allowable moment of inertia (kg·m2) (Note 6) | Allowable torque (N·m) | |||||||||
IX-NNN8020H-①-T2-② 【IX-NNN8040H-①-T2-②】 | 1-Axis | 1st arm | 450 | 750 | ±125 degree | ±0.015 (XY) | 7586mm/s (Resultant speed) | 0.43 | 5 | 20 | 304.0 | 123.0 | 0.1 | 11.7 |
2-Axis | 2nd arm | 350 | 400 | ±145 degree | ||||||||||
3-Axis | Vertical axis | - | 400 | 200mm [400mm] | ±0.010 | 1614mm/s | ||||||||
4-Axis | Rotating shaft | - | 200 | ±360 degree | ±0.005 | 1266 degree/s |
Legend ① Cable length ② Option
Actuator specification
Heading | Contents |
---|---|
Encoder type | Absolute |
User wiring | 25-core AWG26 shielded connector D-sub 25-pin (socket) |
User piping | Air tube (O.D. ø6, I.D. ø4) x 2 (Normal working pressure 0.8 MPa) Air tube (O.D. ø4, I.D. ø2.5) x 2 (Normal working pressure 0.8 MPa) |
Alarm indicator light (Note 7) | 1 small red LED indicator (24V DC supply required) |
Brake release switch (Note 8) | Brake release switch for vertical axis fall prevention (24V DC supply required) |
Ambient temperature/humidity | Temperature 0-40 ℃ Humidity 20-85% RH or less (no condensation) |
Body weight | 60kg |
Cable length (Note 9) | 5L: 5m (standard) 10L: 10m |
Adaptive controller
The actuators introduced in this page are controllable using the controllers shown below. Please select their type based on intended usage.
Name | Appearance | Max. connectable axis No. | Power source voltage | Control method | Maximum positioning points | ||||||||||||||
---|---|---|---|---|---|---|---|---|---|---|---|---|---|---|---|---|---|---|---|
Positioner | Pulse train | Program | Network ※Select | ||||||||||||||||
DV | CC | CIE | PR | CN | ML | ML3 | EC | EP | PRT | SSN | ECM | ||||||||
XSEL-PX4/QX4 | ![]() | 4 | Three-phase AC200V | - | - | ● | ● | ● | - | ● | - | - | - | - | ● | - | - | - | 20000 |
XSEL-RAX4/SAX4 (for IX, IXA) | ![]() | 4 | - | - | ● | ● | ● | - | ● | - | - | - | ● | ● | - | - | - | 36666 (depending on type) |
(Note) Refer to page 7-17 for network abbreviation symbols such as DV and CC.
Oversea specification
(Note) CE is optional.
Important notes on selection
![]() | (1) Refer to page 4-675 for (Note 1) to (Note 10). (2) SCARA robots cannot operate continuously at 100% speed and acceleration. Refer to the technical information on page 1-507 for operating conditions. (3) The numbers noted in [ ] are for models with a vertical axis of 400 mm. Other specifications and dimensions are common for both vertical axis of 200 mm and 400 mm. (4) An adjustment jig is required to perform absolute reset which is needed whenever the encoder absolute data was lost. Refer to page 4-742 for further details. (5) Flange option is available. Refer to page 4-742 for further details. |
Dimension drawing
*1 At 3-M4 depth 8, the pilot hole penetrates the side of the arm.
*2 The external force applied to the spacer should be 30N or less in the axial direction and 2N·m or less in the rotating direction. (For each spacer)
*3 The LED operates when the user takes a signal from the I/O output of the controller and applies 24V DC to the LED terminal in the user wiring.
*4 The height dimension varies depending on the actuator posture at the specified position. The noted value refers to the maximum guideline value.
(Note) Cable/Piping
・Motor ・Encoder cable 5m/10m
・Brake power supply cable 5m/10m
・User wiring cable 5m/10m
・User piping (4 pipes) 0.15m
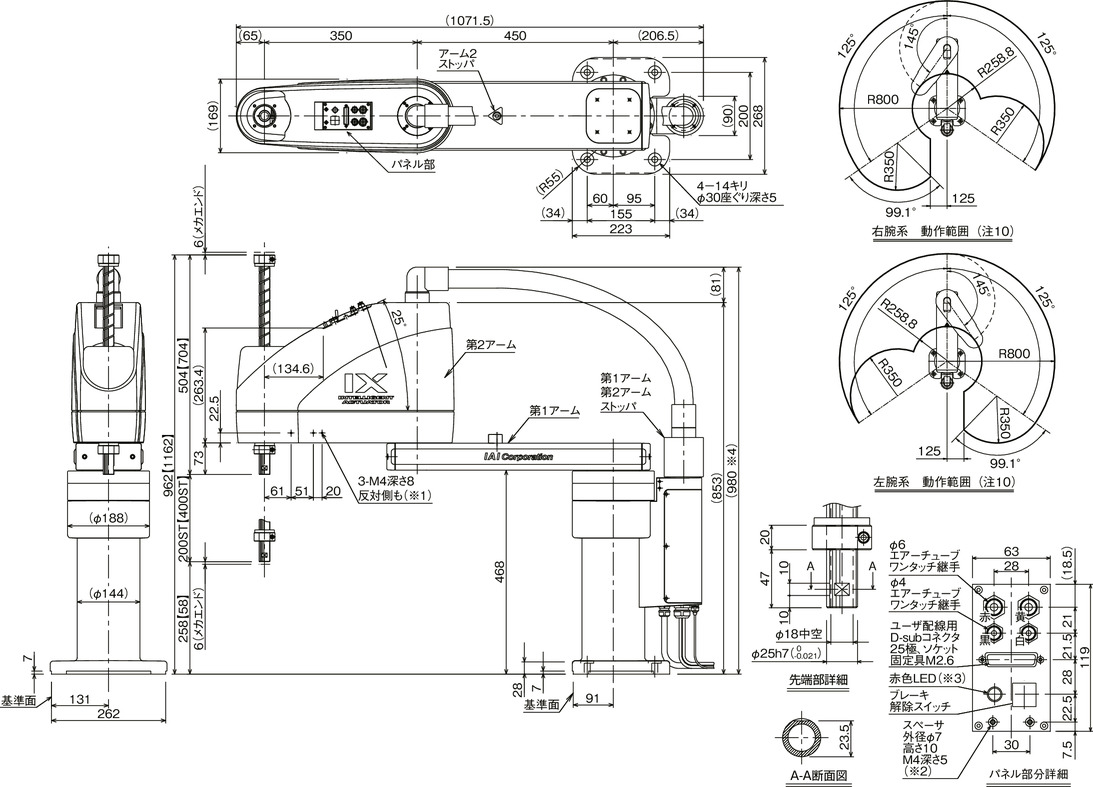