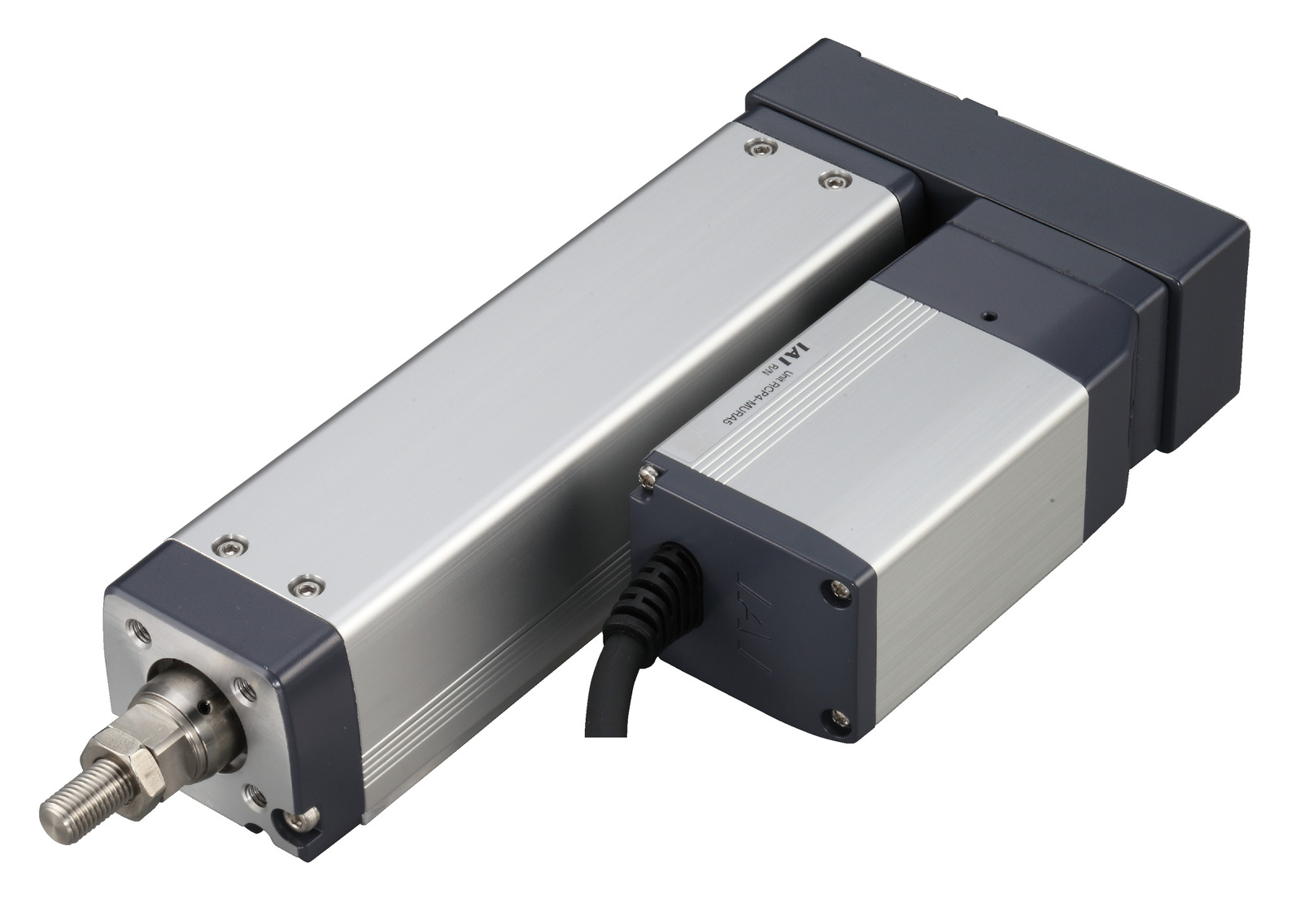
(Note) Photo above shows the motor reversing specification (Motor reversing on the left)(ML).
Actuator specification
Model | Lead (mm) | Connecting controller | Maximum Load Capacity | Maximum pressing force (N) | Stroke (mm) | |
---|---|---|---|---|---|---|
Horizontal (kg) | Vertical (kg) | |||||
RCP4-RA6R-I-56P-24-①-P3-②-③ | 24 | High Output Enabled | 20 | 3 | 182 | 50 - 500 (50mm intervals) |
High Output Disabled | 18 | 3 (Note1) | ||||
RCP4-RA6R-I-56P-16-①-P3-②-③ | 16 | High Output Enabled | 50 | 8 | 273 | |
High Output Disabled | 40 (Note1) | 5 (Note1) | ||||
RCP4-RA6R-I-56P-8-①-P3-②-③ | 8 | High Output Enabled | 60 | 18 | 547 | |
High Output Disabled | 50 (Note1) | 17.5 (Note1) | ||||
RCP4-RA6R-I-56P-4-①-P3-②-③ | 4 | High Output Enabled | 80 | 28 | 1094 | |
High Output Disabled | 55 (Note1) | 26 (Note1) |
Symbol description ① Stroke ② Cable length ③ Option
(Note1) Assumes for 0.2G.
Lead (mm) | Stroke controller | 50 - 500 (50mm intervals) |
---|---|---|
24 | High Output Enabled | 800<600> |
High Output Disabled | 600<400> | |
16 | High Output Enabled | 560 |
High Output Disabled | 420 | |
8 | High Output Enabled | 420<350> |
High Output Disabled | 210 | |
4 | High Output Enabled | 175 |
High Output Disabled | 140 |
(Measured in mm/s)
(Note) The value within < > are applicable for those installed vertically.
(Note) Lead 8 assumes an acceleration of 0.1G.
Correlation diagram of speed and load capacity
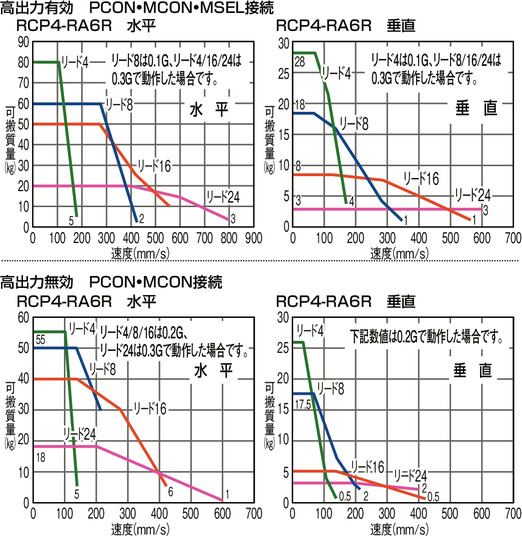
Flexible volume (reference value)
Diagram below shows the flexible volume of a rod when a force is applied to it from its side upon setting the actuator in vertical posture.
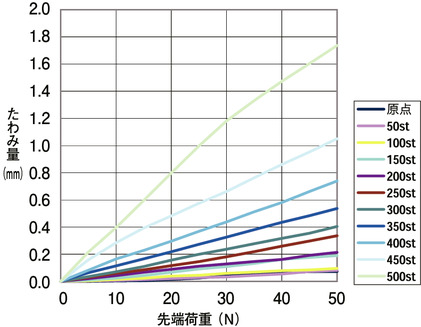
Actuator specification
Heading | Contents |
---|---|
Drive system | Ball screw φ12mm, rolled C10 |
Positioning repeatability (Note4) | ±0.02mm 【±0.03mm】 |
Lost motion | 0.1mm and below |
Rod | φ25mm Stainless tube |
Non-rotational accuracy of rod | 0° |
Allowable load / torque for the rod tip | Refer dimension by stroke table, or page 1-475 of the General Catalogue 2017 |
Rod tip overhanging distance | 100mm and below |
Ambient operating temperature and humidity | 0 - 40℃, RH 85% and below (Non-condensing) |
(Note4) Value shown in 【 】 applies for lead 24.
Adaptive controller
The actuators introduced in this page are controllable using the controllers shown below. Please select their type based on intended usage.
Name | Appearance | Max. connectable axis No. | Power source voltage | Control method | Maximum positioning points | ||||||||||||||
---|---|---|---|---|---|---|---|---|---|---|---|---|---|---|---|---|---|---|---|
Positioner | Pulse train | Program | Network ※Select | ||||||||||||||||
DV | CC | CIE | PR | CN | ML | ML3 | EC | EP | PRT | SSN | ECM | ||||||||
MCON-C/CG | ![]() | 8 | DC24V | - | - | - | ● | ● | ● | ● | ● | - | ● | ● | ● | ● | ● | ● | 256 |
MCON-LC/LCG | ![]() | 6 | - | - | ● | ● | ● | - | ● | ● | - | - | ● | ● | ● | - | - | 256 | |
MSEL-PC/PG | ![]() | 4 | Single phase AC 100 - 230V | - | - | ● | ● | ● | - | ● | - | - | - | ● | ● | ● | - | - | 30000 |
PCON-CB/CGB | ![]() | 1 | DC24V | ● ※Selectable | ● ※Selectable | - | ● | ● | ● | ● | ● | ● | ● | ● | ● | ● | - | - | 512 (768 for network specification) |
PCON-CYB/PLB/POB | ![]() | 1 | ● ※Selectable | ● ※Selectable | - | - | - | - | - | - | - | - | - | - | - | - | - | 64 | |
RCON | ![]() | 16 | - | - | - | ● | ● | ● | ● | - | - | - | ● | ● | ● | - | - | 128 |
(Note) Please refer to page 6 -13 for abbreviated names of network (e.g. DV, CC).
(Note) High-power setting is only available in MCON with an option for "high-power setting specification". Maximum number of axis connectable during high-power is C:4 and LC:3.
Oversea specification
Feature
Important notes on selection
![]() | (1) Value assuming a maximum transfer degree of 0.3G (0.2G for certain models). Refer General Catalogue 2017, page 1-455 for further information. (2) Load capacity and maximum speed of a RCP4 depends on the connected controller. Please refer to 'Actuator specification' for further details. (3) Horizontal load capacity shown assumes an operation running with an external guide. (4) Please refer to page 1-387 of general catalogue 2017 for pressing motion. (5) Radial cylinder comes with a built-in guide. Refer the graph on page 1-475 of the General Catalogue 2017 for load mass allowable. (6) Encoder type box for model item will be "I" for simple absolute as well. (7) An extra precaution may be needed depending on mounting posture. Please refer to page 1-379 for further information. (8) A conversion unit, or a conversion cable is required to connect with RCON. Please refer to page Home for further details. |
Dimension drawing
ME: Mechanical end
SE: Stroke end
※1 Connect a motor/encoder cable.
*2 The rod moves to the ME upon returning to origin, so please take precaution that it may not interfere with anything during the process.
*3 The direction the width between two flats are facing differs by product.
*4 Be sure that no external force is applied on to the main body if it is attached using a front housing or a flange.
(Note) Brake equipped 50 stroke specification can't be used for the motor cover and the flange will interfere each other.
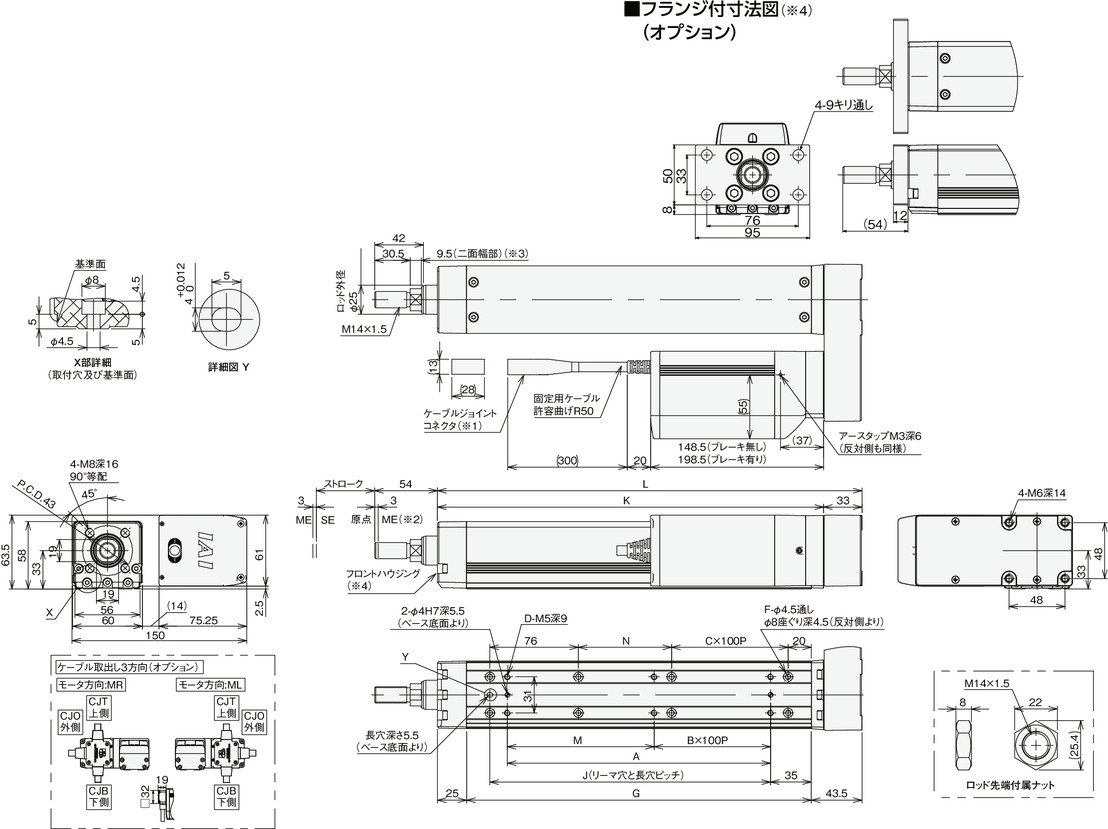
Dimension/Mass by stroke
Stroke | 50 | 100 | 150 | 200 | 250 | 300 | 350 | 400 | 450 | 500 | |
---|---|---|---|---|---|---|---|---|---|---|---|
L | 214.5 | 264.5 | 314.5 | 364.5 | 414.5 | 464.5 | 514.5 | 564.5 | 614.5 | 664.5 | |
A | 76 | 126 | 176 | 226 | 276 | 326 | 376 | 426 | 476 | 526 | |
B | 0 | 0 | 1 | 1 | 2 | 2 | 3 | 3 | 4 | 4 | |
C | 0 | 0 | 0 | 1 | 1 | 2 | 2 | 3 | 3 | 4 | |
D | 4 | 4 | 6 | 6 | 8 | 8 | 10 | 10 | 12 | 12 | |
F | 6 | 6 | 6 | 8 | 8 | 10 | 10 | 12 | 12 | 14 | |
G | 146 | 196 | 246 | 296 | 346 | 396 | 446 | 496 | 546 | 596 | |
J | 91 | 141 | 191 | 241 | 291 | 341 | 391 | 441 | 491 | 541 | |
K | 181.5 | 231.5 | 281.5 | 331.5 | 381.5 | 431.5 | 481.5 | 531.5 | 581.5 | 631.5 | |
M | 76 | 126 | 76 | 126 | 76 | 126 | 76 | 126 | 76 | 126 | |
N | 30 | 80 | 130 | 80 | 130 | 80 | 130 | 80 | 130 | 80 | |
Allowable static load at the rod tip (N) | 112.7 | 91.5 | 76.7 | 65.7 | 57.2 | 50.4 | 44.8 | 40.2 | 36.2 | 32.7 | |
Allowable dynamic load on the rod tip (N) | Load off-set 0mm | 49.0 | 37.4 | 29.9 | 24.5 | 20.4 | 17.1 | 14.5 | 12.3 | 10.3 | 8.6 |
Load off-set 100mm | 38.7 | 31.0 | 25.5 | 21.4 | 18.1 | 15.4 | 13.2 | 11.2 | 9.5 | 8.0 | |
Allowable static torque at the rod tip (Nm) | 11.4 | 9.3 | 7.9 | 6.8 | 6.0 | 5.4 | 4.9 | 4.5 | 4.1 | 3.8 | |
Allowable dynamic torque at the rod tip (N・m) | 3.9 | 3.1 | 2.5 | 2.1 | 1.8 | 1.5 | 1.3 | 1.1 | 1.0 | 0.8 | |
Mass (kg) | Brake present | 3.9 | 4.2 | 4.5 | 4.8 | 5.1 | 5.5 | 5.8 | 6.1 | 6.4 | 6.8 |
Brake absent | 4.4 | 4.7 | 5.0 | 5.3 | 5.6 | 6.0 | 6.3 | 6.6 | 6.9 | 7.3 |