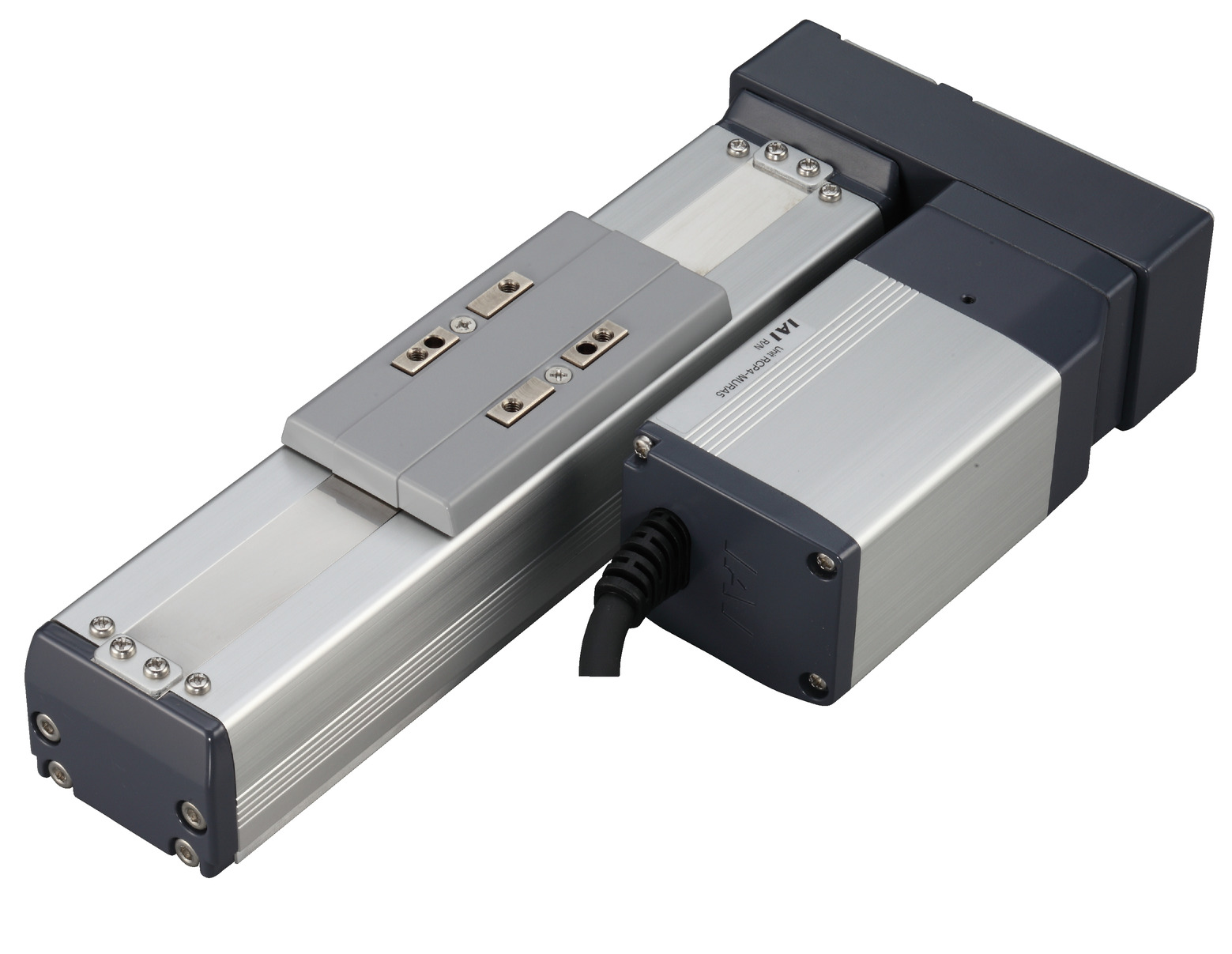
(Note) Photo above shows the motor reversing specification (Motor reversing on the left)(ML).
Actuator specification
Model | Lead (mm) | Connecting controller | Maximum Load Capacity | Stroke (mm) | |
---|---|---|---|---|---|
Horizontal (kg) | Vertical (kg) | ||||
RCP4-SA7R-I-56P-24-①-P3-②-③ | 24 | High Output Enabled | 20 | 3 | 50 - 800 (50mm intervals) |
High Output Disabled | 18 | 2 (Note1) | |||
RCP4-SA7R-I-56P-16-①-P3-②-③ | 16 | High Output Enabled | 40 | 8 | |
High Output Disabled | 35 | 5 (Note1) | |||
RCP4-SA7R-I-56P-8-①-P3-②-③ | 8 | High Output Enabled | 45 | 16 | |
High Output Disabled | 40 | 10 (Note1) | |||
RCP4-SA7R-I-56P-4-①-P3-②-③ | 4 | High Output Enabled | 45 | 25 | |
High Output Disabled | 40 (Note1) | 15 (Note1) |
Symbol description ① Stroke ② Cable length ③ Option
(Note1) Assumes for 0.2G.
Lead (mm) | Stroke controller | 50 - 450 (50mm intervals) | 500 (mm) | 550 (mm) | 600 (mm) | 650 (mm) | 700 (mm) | 750 (mm) | 800 (mm) |
---|---|---|---|---|---|---|---|---|---|
24 | High Output Enabled | 1000 | 890 | 790 | |||||
High Output Disabled | 800<600> | 790<600> | |||||||
16 | High Output Enabled | 840<700> | 750<700> | 655 | 580 | 515 | |||
High Output Disabled | 560 | 515 | |||||||
8 | High Output Enabled | 490 | 430 | 375 | 325 | 290 | 255 | ||
High Output Disabled | 280 | 255 | |||||||
4 | High Output Enabled | 210 | 185 | 160 | 145 | 125 | |||
High Output Disabled | 140 | 125 |
(Measured in mm/s)
(Note) The value within < are applicable for those installed vertically.
(Note) Assumes an acceleration of 0.1G for lead 8 and lead 4.
Correlation diagram of speed and load capacity
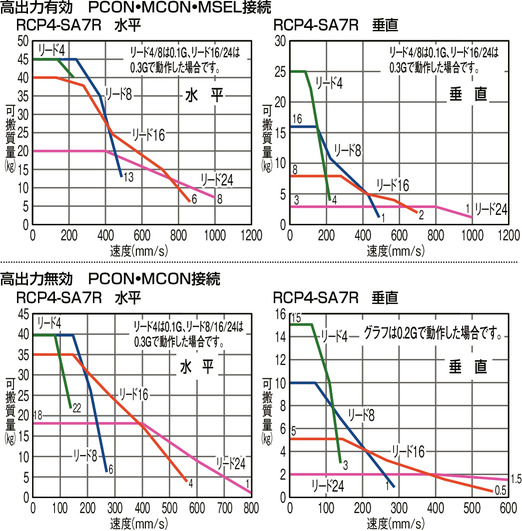
Actuator specification
Heading | Contents |
---|---|
Drive system | Ball screw φ12mm, rolled C10 |
Positioning repeatability (Note3) | ±0.02mm【±0.03mm】 |
Lost motion | 0.1mm and below |
Base | Material: Aluminum (White anodized) |
Allowable static moment value | Ma: 50.4N・m Mb: 71.9N・m Mc: 138N・m |
Allowable dynamic moment (Note4) | Ma: 20.7N・m Mb: 29.6N・m Mc: 56.7N・m |
Ambient operating temperature and humidity | 0 - 40℃, 85% RH Max (Non-condensing) |
(Note3) 【 】 applies to lead 24.
(Note4) Assumes a standard rated life of 5,000km Life time travelling distance differs based on operating condition and attached condition. Please refer to page 1-360 for life time travelling distance.
Adaptive controller
The actuators introduced in this page are controllable using the controllers shown below. Please select their type based on intended usage.
Name | Appearance | Max. connectable axis No. | Power source voltage | Control method | Maximum positioning points | ||||||||||||||
---|---|---|---|---|---|---|---|---|---|---|---|---|---|---|---|---|---|---|---|
Positioner | Pulse train | Program | Network ※Select | ||||||||||||||||
DV | CC | CIE | PR | CN | ML | ML3 | EC | EP | PRT | SSN | ECM | ||||||||
MCON-C/CG | ![]() | 8 | DC24V | - | - | - | ● | ● | ● | ● | ● | - | ● | ● | ● | ● | ● | ● | 256 |
MCON-LC/LCG | ![]() | 6 | - | - | ● | ● | ● | - | ● | ● | - | - | ● | ● | ● | - | - | 256 | |
MSEL-PC/PG | ![]() | 4 | Single phase AC 100 - 230V | - | - | ● | ● | ● | - | ● | - | - | - | ● | ● | ● | - | - | 30000 |
PCON-CB/CGB | ![]() | 1 | DC24V | ● ※Selectable | ● ※Selectable | - | ● | ● | ● | ● | ● | ● | ● | ● | ● | ● | - | - | 512 (768 for network specification) |
PCON-CYB/PLB/POB | ![]() | 1 | ● ※Selectable | ● ※Selectable | - | - | - | - | - | - | - | - | - | - | - | - | - | 64 | |
RCON | ![]() | 16 | - | - | - | ● | ● | ● | ● | - | - | - | ● | ● | ● | - | - | 128 |
(Note) Please refer to page 6 -13 for abbreviated names of network (e.g. DV, CC).
(Note) High-power setting is only available in MCON with an option for "high-power setting specification". Maximum number of axis connectable during high-power is C:4 and LC:3.
Oversea specification
Important notes on selection
![]() | (1) Load capacity shown in "Actuator specification" assumes an operation in acceleration of 0.3G (0.2G for certain models). Nevertheless of the acceleration upper limit, which is 1G (*), load capacity drops when the acceleration increase. (2) Please take note that the maximum load capacity and maximum speed depends on the connected controller. Please refer to 'Actuator specification' for further details. (3) Please refer to page 1-387 of the General Catalogue 2017 for further details of pressing motion. (4) The standard value for offset load lengths are 230mm and below, towards the direction of Ma, Mb and Mc. Please refer to the diagram on page 1-104 for offset load length. (5) Safety measures may be required depending on the attachment orientation. Please refer to page 1-379 for further information. (6) A conversion unit, or a conversion cable is required to connect with RCON. Please refer to page Home for further details. |
Dimension drawing
ME: Mechanical end
SE: Stroke end
※1 Connect a motor/encoder cable. Please refer to page 1- 291 for the further details about the cable.
※2 Ensure the slider does not collide with other items, for it will return to ME after homing process.
※3 Please use the reamer hole (φ4) instead, for there are no slots prepared for 50 stroke.
Please ensure slider attachment and motor unit does not interfere each other if the attachment overhangs above the unit.
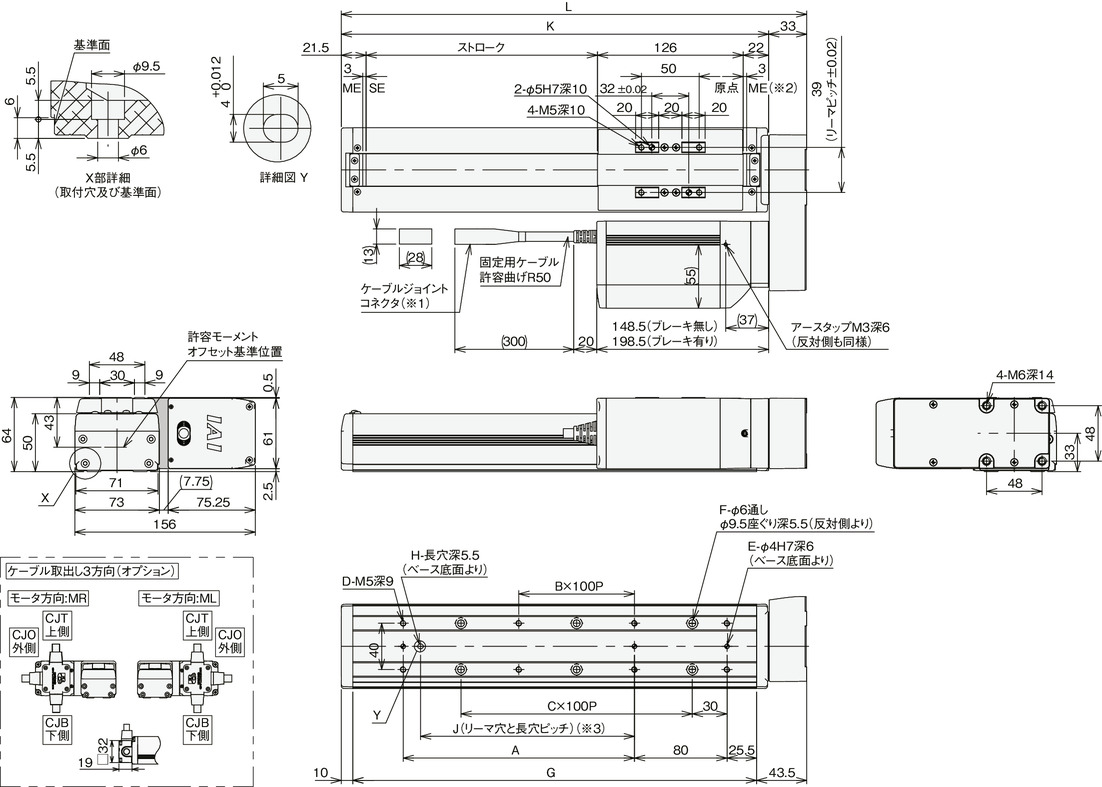
Dimension/Mass by stroke
Stroke | 50 | 100 | 150 | 200 | 250 | 300 | 350 | 400 | 450 | 500 | 550 | 600 | 650 | 700 | 750 | 800 | |
---|---|---|---|---|---|---|---|---|---|---|---|---|---|---|---|---|---|
L | 252.5 | 302.5 | 352.5 | 402.5 | 452.5 | 502.5 | 552.5 | 602.5 | 652.5 | 702.5 | 752.5 | 802.5 | 852.5 | 902.5 | 952.5 | 1002.5 | |
A | 0 | 100 | 100 | 200 | 200 | 300 | 300 | 400 | 400 | 500 | 500 | 600 | 600 | 700 | 700 | 800 | |
B | 0 | 0 | 0 | 1 | 1 | 2 | 2 | 3 | 3 | 4 | 4 | 5 | 5 | 6 | 6 | 7 | |
C | 1 | 1 | 2 | 2 | 3 | 3 | 4 | 4 | 5 | 5 | 6 | 6 | 7 | 7 | 8 | 8 | |
D | 4 | 6 | 6 | 8 | 8 | 10 | 10 | 12 | 12 | 14 | 14 | 16 | 16 | 18 | 18 | 20 | |
E | 2 | 3 | 3 | 3 | 3 | 3 | 3 | 3 | 3 | 3 | 3 | 3 | 3 | 3 | 3 | 3 | |
F | 4 | 4 | 6 | 6 | 8 | 8 | 10 | 10 | 12 | 12 | 14 | 14 | 16 | 16 | 18 | 18 | |
G | 199 | 249 | 299 | 349 | 399 | 449 | 499 | 549 | 599 | 649 | 699 | 749 | 799 | 849 | 899 | 949 | |
H | 0 | 1 | 1 | 1 | 1 | 1 | 1 | 1 | 1 | 1 | 1 | 1 | 1 | 1 | 1 | 1 | |
J | 0 | 85 | 85 | 185 | 185 | 285 | 285 | 385 | 385 | 485 | 485 | 585 | 585 | 685 | 685 | 785 | |
K | 219.5 | 269.5 | 319.5 | 369.5 | 419.5 | 469.5 | 519.5 | 569.5 | 619.5 | 669.5 | 719.5 | 769.5 | 819.5 | 869.5 | 919.5 | 969.5 | |
Mass (kg) | Brake present | 3.8 | 4.0 | 4.3 | 4.5 | 4.8 | 5.0 | 5.3 | 5.5 | 5.7 | 6.0 | 6.2 | 6.5 | 6.7 | 7.0 | 7.2 | 7.4 |
Brake absent | 4.3 | 4.5 | 4.8 | 5.0 | 5.3 | 5.5 | 5.8 | 6.0 | 6.2 | 6.5 | 6.7 | 7.0 | 7.2 | 7.5 | 7.7 | 8.0 |