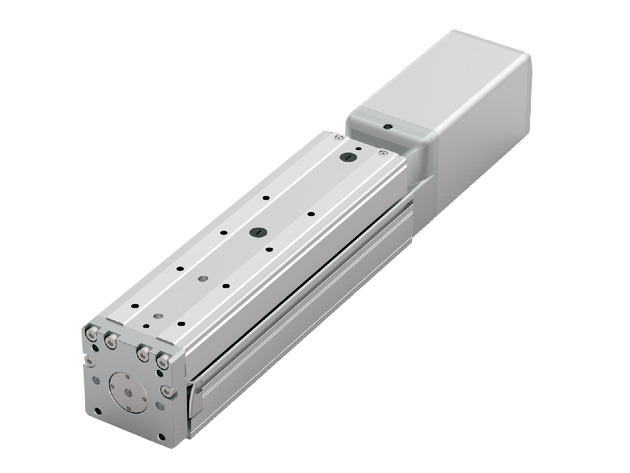
メインスペック
項目 | 内容 | |||||
---|---|---|---|---|---|---|
リード | ボールねじリード(mm) | 24 | 16 | 8 | 4 | |
水平 | 可搬質量 | 最大可搬質量(kg)(高出力有効) | 10 | 12 | 15 | 15 |
最大可搬質量(kg)(高出力無効) | 10 | 12 | 15 | 15 | ||
速度/加減速度 | 最高速度(mm/s) | 1080 | 700 | 420 | 210 | |
最低速度(mm/s) | 30 | 20 | 10 | 5 | ||
定格加減速度(G) | 0.5 | 0.5 | 1 | 1 | ||
最高加減速度(G) | 1 | 1 | 1 | 1 | ||
垂直 | 可搬質量 | 最大可搬質量(kg)(高出力有効) | 3 | 7 | 16 | 20 |
最大可搬質量(kg)(高出力無効) | 3 | 5 | 12 | 20 | ||
速度/加減速度 | 最高速度(mm/s) | 860 | 560 | 350 | 210 | |
最低速度(mm/s) | 30 | 20 | 10 | 5 | ||
定格加減速度(G) | 0.5 | 0.5 | 0.1 | 0.5 | ||
最高加減速度(G) | 0.5 | 0.5 | 0.5 | 0.5 | ||
押付け | 押付け時最大推力(N) | 139 | 209 | 418 | 836 | |
押付け最高速度(mm/s) | 20 | 20 | 20 | 20 | ||
ブレーキ | ブレーキ仕様 | 無励磁作動電磁ブレーキ | ||||
ブレーキ保持力(kgf) | 3 | 7 | 16 | 20 | ||
ストローク | 最小ストローク(mm) | 25 | 25 | 25 | 25 | |
最大ストローク(mm) | 300 | 300 | 300 | 300 | ||
ストロークピッチ(mm)(注1) | 50 | 50 | 50 | 50 |
(注1) ストローク25~200の間のみ25間隔です。
項目 | 内容 |
---|---|
駆動方式 | ボールねじ φ12mm 転造C10 |
繰返し位置決め精度 | ±0.01mm |
ロストモーション | 0.1mm以下 |
ベース | 材質:アルミ 白色アルマイト処理 |
リニアガイド | 直動無限循環型 |
静的許容モーメント | Ma:115N・m |
Mb:115N・m | |
Mc:229N・m | |
動的許容モーメント (注2) | Ma:44N・m |
Mb:44N・m | |
Mc:89N・m | |
使用周囲温度・湿度 | 0~40℃、85%RH以下(結露なきこと) |
保護等級 | - |
耐振動・耐衝撃 | 4.9m/s2 |
海外対応規格 | CEマーク、RoHS指令 |
モーター種類 | パルスモーター |
エンコーダー種類 | バッテリーレスアブソリュート |
エンコーダーパルス数 | 8192 pulse/rev |
納期 | ホームページ[納期照会]に記載 |
(注2) 基準定格寿命5,000kmの場合です。走行寿命は運転条件、取付け状態によって異なります。1-180ページにて走行寿命をご確認ください。
テーブルタイプモーメント方向

速度・加速度別可搬質量表
高出力設定有効 可搬質量の単位はkgです。空欄は動作不可となります。
姿勢 | 水平 | 垂直 | ||||||
---|---|---|---|---|---|---|---|---|
速度 | 加速度(G) | |||||||
(mm/s) | 0.1 | 0.3 | 0.5 | 0.7 | 1 | 0.1 | 0.3 | 0.5 |
0 | 10 | 10 | 10 | 8 | 8 | 3 | 3 | 3 |
200 | 10 | 10 | 10 | 8 | 8 | 3 | 3 | 3 |
420 | 10 | 10 | 10 | 8 | 8 | 3 | 3 | 3 |
640 | 10 | 10 | 8 | 7 | 3 | 3 | ||
860 | 9 | 7 | 6 | 3 | 1.5 | 1 | ||
1080 | 3.5 | 2 |
姿勢 | 水平 | 垂直 | ||||||
---|---|---|---|---|---|---|---|---|
速度 | 加速度(G) | |||||||
(mm/s) | 0.1 | 0.3 | 0.5 | 0.7 | 1 | 0.1 | 0.3 | 0.5 |
0 | 12 | 12 | 12 | 10 | 10 | 7 | 7 | 7 |
140 | 12 | 12 | 12 | 10 | 10 | 7 | 7 | 7 |
280 | 12 | 12 | 12 | 10 | 10 | 7 | 7 | 6 |
420 | 12 | 12 | 12 | 10 | 8 | 6 | 5 | 4 |
560 | 12 | 10 | 8 | 5 | 3 | 2 | ||
700 | 10 | 6 | 3 | 2 |
姿勢 | 水平 | 垂直 | ||||||
---|---|---|---|---|---|---|---|---|
速度 | 加速度(G) | |||||||
(mm/s) | 0.1 | 0.3 | 0.5 | 0.7 | 1 | 0.1 | 0.3 | 0.5 |
0 | 15 | 15 | 15 | 15 | 15 | 16 | 14 | 12 |
70 | 15 | 15 | 15 | 15 | 15 | 16 | 14 | 12 |
140 | 15 | 15 | 15 | 15 | 12 | 16 | 14 | 10 |
210 | 15 | 15 | 15 | 12 | 10 | 12 | 10 | 8 |
280 | 15 | 15 | 12 | 10 | 8 | 9 | 8 | 6 |
350 | 12 | 10 | 8 | 6 | ||||
420 | 8 |
姿勢 | 水平 | 垂直 | ||||||
---|---|---|---|---|---|---|---|---|
速度 | 加速度(G) | |||||||
(mm/s) | 0.1 | 0.3 | 0.5 | 0.7 | 1 | 0.1 | 0.3 | 0.5 |
0 | 15 | 15 | 15 | 15 | 15 | 20 | 20 | 20 |
35 | 15 | 15 | 15 | 15 | 15 | 20 | 20 | 20 |
70 | 15 | 15 | 15 | 15 | 15 | 20 | 18 | 14 |
105 | 15 | 15 | 15 | 15 | 12 | 18 | 16 | 10 |
140 | 15 | 15 | 15 | 12 | 10 | 16 | 12 | 6 |
175 | 15 | 12 | 10 | 10 | 6 | |||
210 | 10 | 6 |
高出力設定無効 可搬質量の単位はkgです。空欄は動作不可となります。
姿勢 | 水平 | 垂直 | |
---|---|---|---|
速度 | 加速度(G) | ||
(mm/s) | 0.3 | 0.7 | 0.3 |
0 | 10 | 8 | 3 |
200 | 10 | 8 | 3 |
420 | 10 | 8 | 3 |
640 | 5 | 1 | |
860 | 1 |
姿勢 | 水平 | 垂直 | |
---|---|---|---|
速度 | 加速度(G) | ||
(mm/s) | 0.3 | 0.7 | 0.3 |
0 | 12 | 10 | 5 |
140 | 12 | 10 | 5 |
280 | 12 | 10 | 5 |
420 | 12 | 4 | |
560 | 5 |
姿勢 | 水平 | 垂直 | |
---|---|---|---|
速度 | 加速度(G) | ||
(mm/s) | 0.3 | 0.7 | 0.3 |
0 | 15 | 15 | 12 |
70 | 15 | 15 | 12 |
140 | 15 | 15 | 12 |
210 | 15 | 12 | 3.5 |
280 | 10 |
姿勢 | 水平 | 垂直 | |
---|---|---|---|
速度 | 加速度(G) | ||
(mm/s) | 0.3 | 0.7 | 0.3 |
0 | 15 | 15 | 20 |
35 | 15 | 15 | 20 |
70 | 15 | 15 | 18 |
105 | 15 | 13 | 10 |
140 | 6 |
ストロークと最高速度
(単位はmm/s)
リード (mm) | 接続 コントローラー | 25~300 (mm) |
---|---|---|
24 | 高出力有効 | 1080<860> |
高出力無効 | 860<420> | |
16 | 高出力有効 | 700<560> |
高出力無効 | 560<280> | |
8 | 高出力有効 | 420<350> |
高出力無効 | 280<210> | |
4 | 高出力有効 | 210 |
高出力無効 | 140<105> |
(注) < >内は垂直使用の場合です。
押付け力と電流制限値の相関図
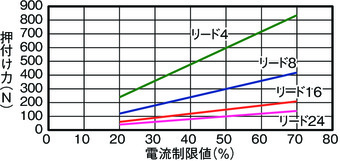
ストローク別許容負荷質量
(注) 許容負荷質量の算出の条件:加速度によるモーメントを考慮したガイド走行寿命5,000kmとなる負荷重量(加速度0.5G、速度500m/s)
水平 平置き
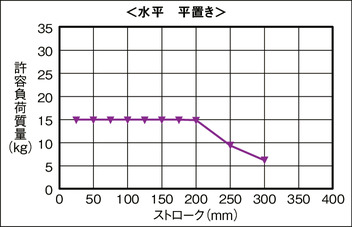
水平 横立て
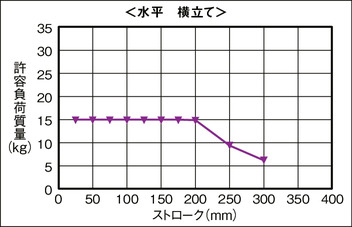
垂直
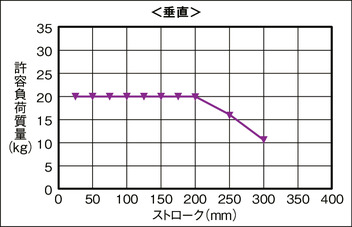
適応コントローラー
本ページのアクチュエーターは下記のコントローラーで動作が可能です。ご使用になる用途に応じたタイプをご選択ください。
名称 | 外観 | 最大接続 可能軸数 | 電源電圧 | 制御方法 | 最大位置決め点数 | ||||||||||||||
---|---|---|---|---|---|---|---|---|---|---|---|---|---|---|---|---|---|---|---|
ポジショナー | パルス列 | プログラム | ネットワーク ※選択 | ||||||||||||||||
DV | CC | CIE | PR | CN | ML | ML3 | EC | EP | PRT | SSN | ECM | ||||||||
MCON-C/CG | ![]() | 8 | DC24V | - | - | - | ● | ● | ● | ● | ● | - | ● | ● | ● | ● | ● | ● | 256 |
MSEL-PC/PG | ![]() | 4 | 単相AC 100~230V | - | - | ● | ● | ● | - | ● | - | - | - | ● | ● | ● | - | - | 30000 |
PCON-CB/CGB | ![]() | 1 | DC24V | ● ※選択 | ● ※選択 | - | ● | ● | ● | ● | ● | ● | ● | ● | ● | ● | - | - | 512 (ネットワーク仕様は768) |
PCON-CYB/PLB/POB | ![]() | 1 | ● ※選択 | ● ※選択 | - | - | - | - | - | - | - | - | - | - | - | - | - | 64 | |
RCON | ![]() | 16 | - | - | - | ● | ● | ● | ● | - | - | - | ● | ● | ● | - | - | 128 | |
RSEL | ![]() | 8 | - | - | ● | ● | ● | ● | ● | - | - | - | ● | ● | ● | - | - | 36000 |
(注) DV、CCなどのネットワーク略称記号については、7-17ページをご確認ください。
(注) RCP6Sシリーズの内蔵コントローラーは、7-103ページをご確認ください。
(注) MCONはオプションで「高出力設定仕様」を指定したものに限り、高出力有効の設定が可能です。高出力有効時の最大接続可能軸数はC:4、LC:3です。
海外規格
選定上の注意
![]() | (1)「メインスペック」の可搬質量は、最大値を表示しています。詳細は「速度・加速度別可搬質量表」をご参照ください。 (2)押付け動作を行う場合は「押付け力と電流制限値の相関図」をご参照ください。押付け力は目安の値です。注意点は1-269ページをご確認ください。 (3)RCP6S(コントローラー内蔵)のリード4/8/16 は、使用周囲温度によって、デューティーの制限が必要です。詳細は1-286ページをご参照ください。 (4)取付姿勢によっては注意が必要です。詳細は1-199ページをご参照ください。 (5)張出し負荷長は、動的許容モーメントの範囲内としてください。 (6)テーブルの変位量は、取扱説明書をご参照ください。 (7)許容負荷質量は機械的制限によりストロークが長くなると低下します。詳細は「ストローク別許容負荷質量」をご参照ください。 (8)静的許容モーメントは、テーブルの上面かつガイドブロック真上(許容モーメントオフセット基準位置)におけるリニアガイドの許容値です。詳細は1-179ページをご確認ください。 |
寸法図
RCP6-TA7C(シングルブロック仕様)
ST:ストローク
M.E.:メカニカルエンド
S.E.:ストロークエンド
(注) 原点復帰を行った場合はテーブルがM.E.まで移動しますので周囲物との干渉にご注意ください。
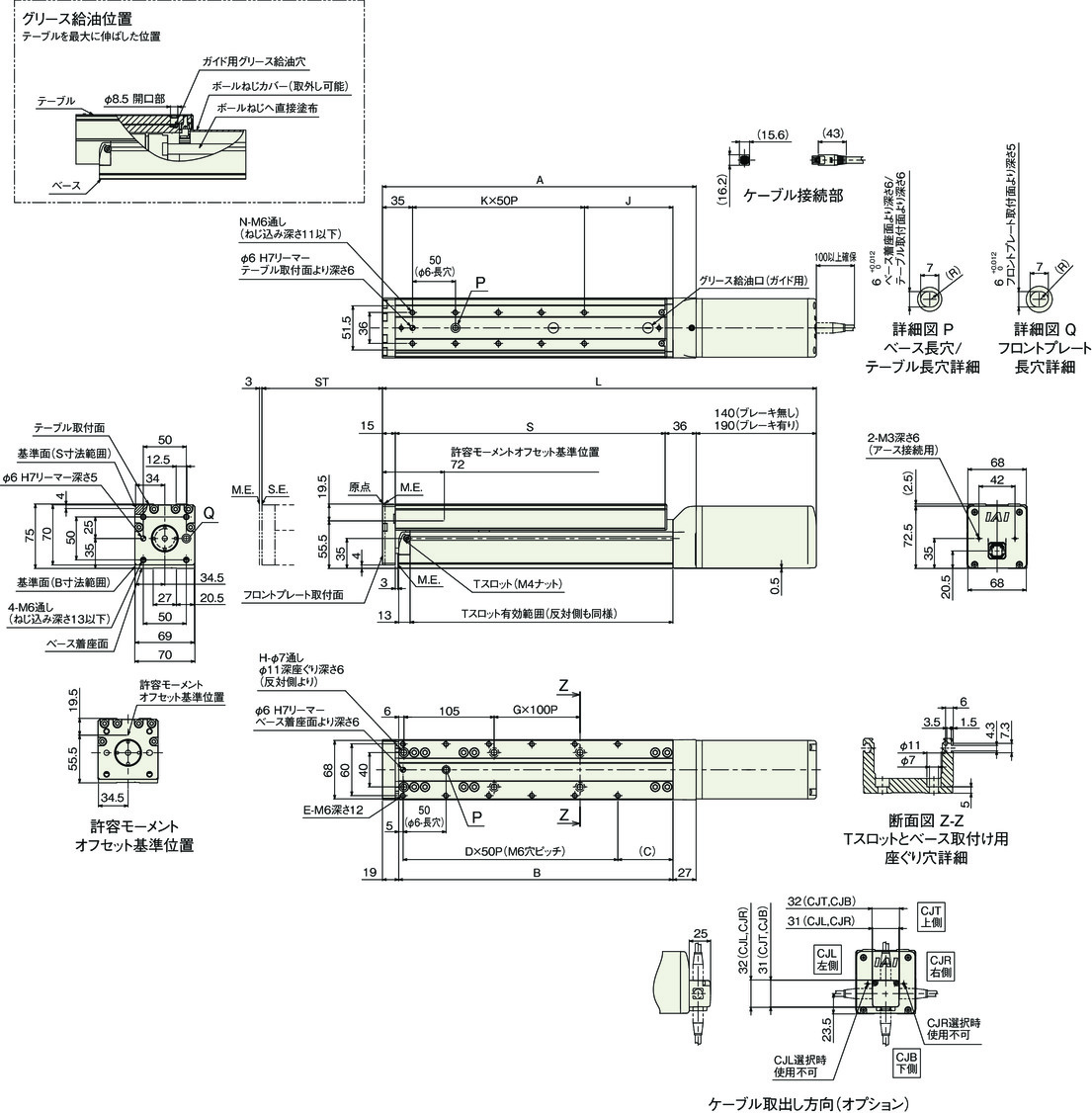
ストローク別寸法
ストローク | 25 | 50 | 75 | 100 | 125 | 150 | 175 | 200 | 250 | 300 | |
---|---|---|---|---|---|---|---|---|---|---|---|
L | ブレーキ無し | 330 | 355 | 380 | 405 | 430 | 455 | 480 | 505 | 555 | 605 |
ブレーキ有り | 380 | 405 | 430 | 455 | 480 | 505 | 530 | 555 | 605 | 655 | |
A | 190 | 215 | 240 | 265 | 290 | 315 | 340 | 365 | 415 | 465 | |
B | 144 | 169 | 194 | 219 | 244 | 269 | 294 | 319 | 369 | 419 | |
C | 39 | 64 | 39 | 64 | 39 | 64 | 39 | 64 | 64 | 64 | |
D | 2 | 2 | 3 | 3 | 4 | 4 | 5 | 5 | 6 | 7 | |
E | 6 | 6 | 8 | 8 | 10 | 10 | 12 | 12 | 14 | 16 | |
G | 0 | 0 | 0 | 0 | 1 | 1 | 1 | 1 | 2 | 2 | |
H | 4 | 4 | 4 | 4 | 6 | 6 | 6 | 6 | 8 | 8 | |
J | 78 | 103 | 78 | 103 | 78 | 103 | 78 | 103 | 103 | 103 | |
K | 1 | 1 | 2 | 2 | 3 | 3 | 4 | 4 | 5 | 6 | |
N | 4 | 4 | 6 | 6 | 8 | 8 | 10 | 10 | 12 | 14 | |
S | 139 | 164 | 189 | 214 | 239 | 264 | 289 | 314 | 364 | 414 |
ストローク別質量
ストローク | 25 | 50 | 75 | 100 | 125 | 150 | 175 | 200 | 250 | 300 | |
---|---|---|---|---|---|---|---|---|---|---|---|
質量 (kg) | ブレーキ無し | 3.9 | 4.1 | 4.3 | 4.5 | 4.7 | 5.0 | 5.2 | 5.4 | 5.8 | 6.3 |
ブレーキ有り | 4.3 | 4.5 | 4.7 | 5.0 | 5.2 | 5.4 | 5.6 | 5.8 | 6.3 | 6.7 |
RCP6S-TA7C(シングルブロック仕様)
ST:ストローク
M.E.:メカニカルエンド
S.E.:ストロークエンド
(注) 原点復帰を行った場合はテーブルがM.E.まで移動しますので周囲物との干渉にご注意ください。
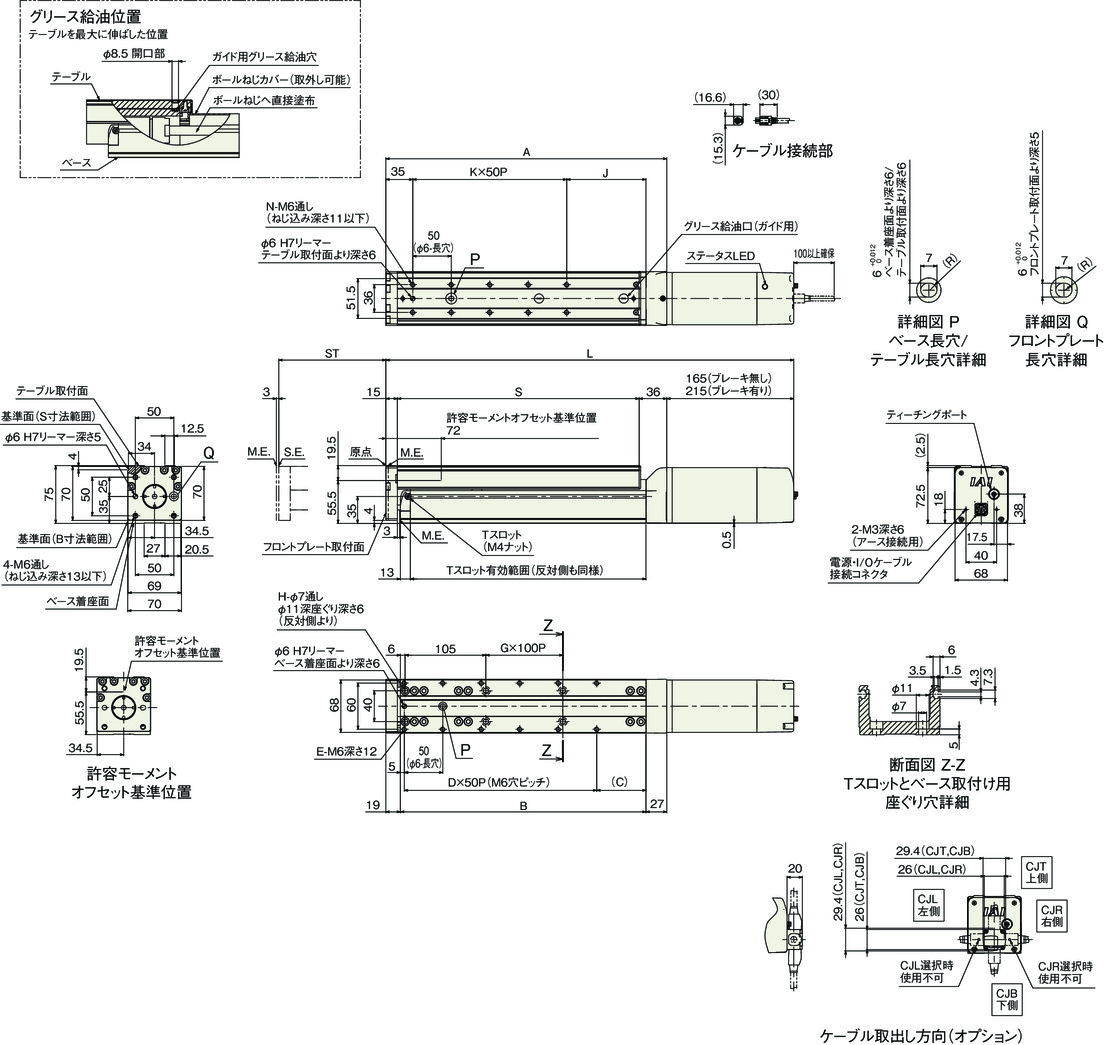
ストローク別寸法
ストローク | 25 | 50 | 75 | 100 | 125 | 150 | 175 | 200 | 250 | 300 | |
---|---|---|---|---|---|---|---|---|---|---|---|
L | ブレーキ無し | 355 | 380 | 405 | 430 | 455 | 480 | 505 | 530 | 580 | 630 |
ブレーキ有り | 405 | 430 | 455 | 480 | 505 | 530 | 555 | 580 | 630 | 680 | |
A | 190 | 215 | 240 | 265 | 290 | 315 | 340 | 365 | 415 | 465 | |
B | 144 | 169 | 194 | 219 | 244 | 269 | 294 | 319 | 369 | 419 | |
C | 39 | 64 | 39 | 64 | 39 | 64 | 39 | 64 | 64 | 64 | |
D | 2 | 2 | 3 | 3 | 4 | 4 | 5 | 5 | 6 | 7 | |
E | 6 | 6 | 8 | 8 | 10 | 10 | 12 | 12 | 14 | 16 | |
G | 0 | 0 | 0 | 0 | 1 | 1 | 1 | 1 | 2 | 2 | |
H | 4 | 4 | 4 | 4 | 6 | 6 | 6 | 6 | 8 | 8 | |
J | 78 | 103 | 78 | 103 | 78 | 103 | 78 | 103 | 103 | 103 | |
K | 1 | 1 | 2 | 2 | 3 | 3 | 4 | 4 | 5 | 6 | |
N | 4 | 4 | 6 | 6 | 8 | 8 | 10 | 10 | 12 | 14 | |
S | 139 | 164 | 189 | 214 | 239 | 264 | 289 | 314 | 364 | 414 |
ストローク別質量
ストローク | 25 | 50 | 75 | 100 | 125 | 150 | 175 | 200 | 250 | 300 | |
---|---|---|---|---|---|---|---|---|---|---|---|
質量 (kg) | ブレーキ無し | 4.0 | 4.3 | 4.5 | 4.7 | 4.9 | 5.1 | 5.3 | 5.6 | 6.0 | 6.4 |
ブレーキ有り | 4.5 | 4.7 | 4.9 | 5.1 | 5.3 | 5.6 | 5.8 | 6.0 | 6.4 | 6.9 |