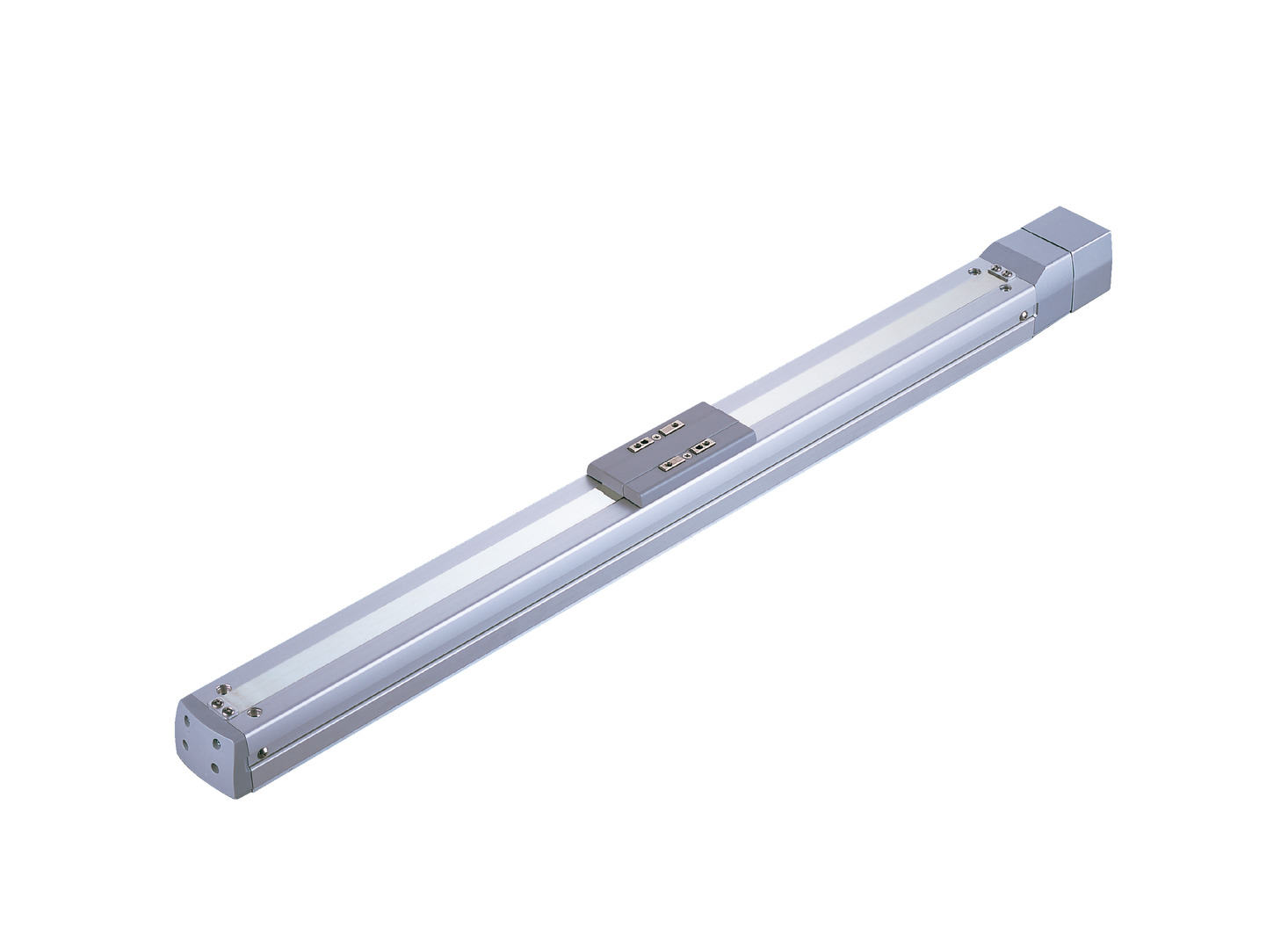
Actuator specification
Model | Motor output (W) | Lead (mm) | Maximum Load Capacity | Rated thrust (N) | Stroke (mm) | |
---|---|---|---|---|---|---|
Horizontal (kg) | Vertical (kg) | |||||
RCS2-SA6D-①-30-12-②-T2-③-④ | 30 | 12 | 6 | 1.5 | 24.2 | 50 - 600 (50mm intervals) |
RCS2-SA6D-①-30-6-②-T2-③-④ | 6 | 12 | 3 | 48.4 | ||
RCS2-SA6D-①-30-3-②-T2-③-④ | 3 | 18 | 6 | 96.8 |
Symbol description ① Encoder type ② Stroke ③ Cable length ④ Option
Stroke lead | 50 - 450 (50mm intervals) | 500 (mm) | 550 (mm) | 600 (mm) |
---|---|---|---|---|
12 | 800 | 760 | 640 | 540 |
6 | 400 | 380 | 320 | 270 |
3 | 200 | 190 | 160 | 135 |
(Measured in mm/s)
Actuator specification
Heading | Contents |
---|---|
Drive system | Ball screw φ10mm, rolled C10 |
Accuracy of Repeating Positioning. | ±0.02mm |
Lost motion | 0.1mm and below |
Base | Base Aluminum, with white alumite treatment |
Allowable static moment value | Ma:38.3N・m Mb:54.7N・m Mc:81.0N・m |
Allowable dynamic moment (Note1) | Ma:11.6N・m Mb:16.6N・m Mc:24.6N・m |
Ambient operating temperature and humidity | 0 - 40℃, 85% RH Max (Non-condensing) |
(Note1) Values shown are for basic rated life of 5,000km. Life time travelling distance differs based on operating condition and attached condition.
Please refer to page 1-360 for life time travelling distance.
Adaptive controller
The actuators introduced in this page are controllable using the controllers shown below. Please select their type based on intended usage.
Name | Appearance | Max. connectable axis No. | Power source voltage | Control method | Maximum positioning points | |||||||||||||
---|---|---|---|---|---|---|---|---|---|---|---|---|---|---|---|---|---|---|
Positioner | Pulse train | Program | Network ※Select | |||||||||||||||
DV | CC | PR | CN | ML | ML3 | EC | EP | PRT | SSN | ECM | ||||||||
MSCON-C | ![]() | 6 | Single phase AC 100V/200V | - | - | - | ● | ● | ● | ● | - | - | ● | ● | - | - | - | 256 |
SCON-CAL/CGAL | ![]() | 1 | ● | - | - | ● | ● | ● | ● | ● | - | ● | ● | ● | - | - | 512 (768 for network specification) | |
SCON-CB/CGB | ![]() | 1 | ● | ● | - | ● | ● | ● | ● | ● | ● | ● | ● | ● | - | - | 512 (768 for network specification) | |
SCON-LC/LCG | ![]() | 1 | - | - | ● | ● | ● | ● | ● | ● | - | ● | ● | ● | - | - | 512 (768 for network specification) | |
SSEL-CS | ![]() | 2 | ● | - | ● | ● | ● | ● | - | - | - | - | ● | - | - | - | 20000 | |
XSEL-P/Q | ![]() | 6 | Single phase AC200V Three-phase AC200V | - | - | ● | ● | ● | ● | - | - | - | - | ● | - | - | - | 20000 |
XSEL-RA/SA | ![]() | 8 | - | - | ● | ● | ● | ● | - | - | - | ● | ● | - | - | - | 55000 (Vary based on type) |
(Note) Please refer to page 6 -13 for abbreviated names of network (e.g. DV, CC).
Oversea specification
(Note) CE is optional.
Important notes on selection
![]() | (1) When the stroke increases, the maximum speed will drop to prevent the ball screw from reaching the critical rotational speed. Use the "Stroke and Max.speed" to check the maximum speed at the stroke you desire. (2) Load capacity shown assumes an operation in 0.3G (0.2G for lead 3), which is the upper limit of acceleration. (3) Available duty depends on the operating condition (e.g.load mass, acceleration/deceleration). Please refer to page 1-448 for further details. (4) The standard value for offset load lengths are 220mm and below, towards the direction of Ma, Mb and Mc. Please refer to the diagram on page 1-104 for offset load length. (5) Safety measures may be required depending on the attachment orientation. Please refer to page 1-379 for further information. |
Dimension drawing
ME: Mechanical end
SE: Stroke end
※1 Connect a motor/encoder cable. Please refer to page 1- 295 for the further details about the cable.
※2 Ensure the slider does not collide with other items, for it will return to ME after homing process.
(Note) There will be an additional length (L) of 26.5mm (39.8mm if wiring exits from the end) and additional mass of 0.3kg.
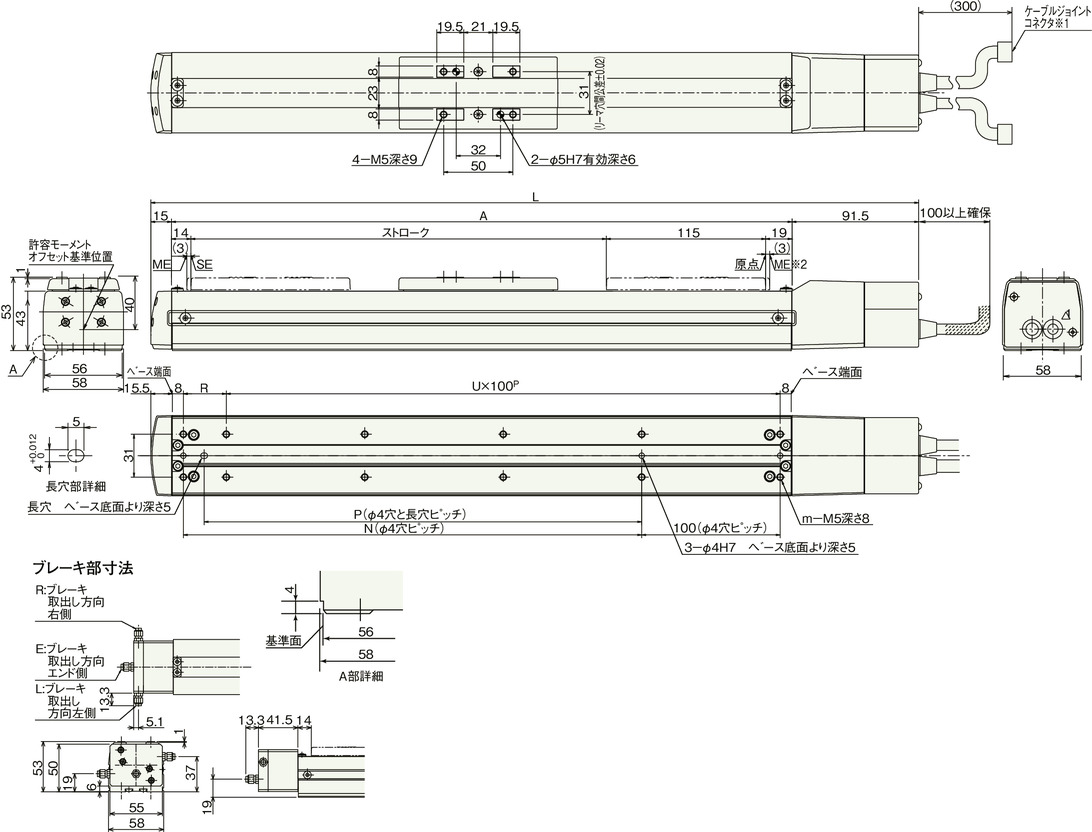
Dimension/Mass by stroke
Stroke | 50 | 100 | 150 | 200 | 250 | 300 | 350 | 400 | 450 | 500 | 550 | 600 |
---|---|---|---|---|---|---|---|---|---|---|---|---|
L | 304.5 | 354.5 | 404.5 | 454.5 | 504.5 | 554.5 | 604.5 | 654.5 | 704.5 | 754.5 | 804.5 | 854.5 |
A | 198 | 248 | 298 | 348 | 398 | 448 | 498 | 548 | 598 | 648 | 698 | 748 |
N | 81 | 131 | 181 | 231 | 281 | 331 | 381 | 431 | 481 | 531 | 581 | 631 |
P | 66 | 116 | 166 | 216 | 266 | 316 | 366 | 416 | 466 | 516 | 566 | 616 |
R | 81 | 31 | 81 | 31 | 81 | 31 | 81 | 31 | 81 | 31 | 81 | 31 |
U | 1 | 2 | 2 | 3 | 3 | 4 | 4 | 5 | 5 | 6 | 6 | 7 |
m | 6 | 8 | 8 | 10 | 10 | 12 | 12 | 14 | 14 | 16 | 16 | 18 |
Mass (kg) | 1.3 | 1.5 | 1.7 | 1.9 | 2.1 | 2.3 | 2.5 | 2.7 | 2.9 | 3.1 | 3.3 | 3.5 |