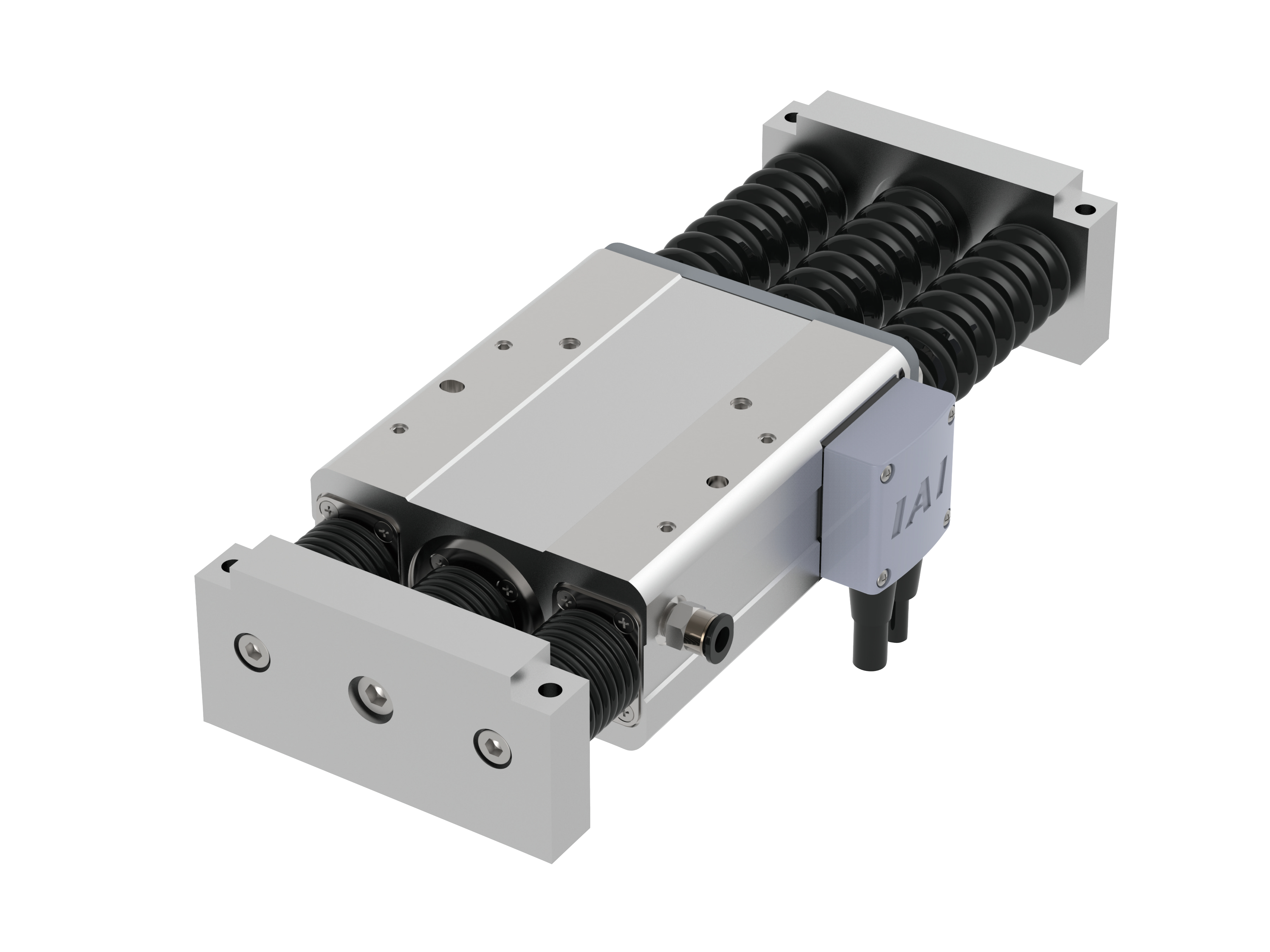
Main specification
Heading | Contents | ||||
---|---|---|---|---|---|
Lead | Ball screw lead (mm) | 10 | 5 | 2.5 | |
Horizontal | Load capacity | Maximum load capacity (kg) | 5 | 10 | 20 |
Speed/ Acceleration/Deceleration | Maximum speed (mm/s) | 380 | 250 | 125 | |
Rated acceleration/deceleration (G) | 0.3 | 0.3 | 0.2 | ||
Maximum acceleration/deceleration (G) | 0.3 | 0.3 | 0.2 | ||
Vertical | Load capacity (Note 1) | Maximum load capacity (kg) | 1.5 | 3 | 6 |
Speed/ Acceleration/Deceleration | Maximum speed (mm/s) | 330 | 250 | 125 | |
Rated acceleration/deceleration (G) | 0.2 | 0.2 | 0.2 | ||
Maximum acceleration/deceleration (G) | 0.2 | 0.2 | 0.2 | ||
Thrust | Rated thrust (N) | 89 | 178 | 356 | |
Cleanroom Compatible | Suction pressure (kPa) | 1 | 1 | 1 | |
Stroke | Minimum stroke (mm) | 50 | 50 | 50 | |
Maximum stroke (mm) | 75 | 75 | 75 | ||
Stroke pitch (mm) | 25 | 25 | 25 |
(Note 1) Value when the main body is fixed.
Heading | Contents |
---|---|
Drive system | Ball screw φ8mm, rolled C10 |
Accuracy of Repeating Positioning. | ±0.02mm |
Lost motion | 0.1mm or less |
Frame | Base: Aluminum, with white alumite treatment |
Cleanliness | Class 100 (0.1μm, Fed.Std.209D) |
Life time traveling distance | 5000km, or 50 million round trips |
Ambient operating temperature and humidity | 0 - 40℃, RH 85% and below (no condensation) |
Protection grade | IP30 |
Vibration resistant/Shock resistant | 4.9m/s2 |
Compatible to overseas standards | CE mark, RoHS compliant |
Motor type | AC servo motor |
Encoder type | Incremental |
Encoder pulse No. | 1600pulse/rev |
Delivery | Written in [Reference for delivery] section of the homepage |
Stroke and maximum speed
(Measured in mm/s)
Stroke lead | 50 (mm) | 75 (mm) |
---|---|---|
10 | 280<230> | 380<330> |
5 | 250<230> | 250 |
2.5 | 125 |
(Note) < > is applicable when operated vertically.
Adaptive controller
The actuators introduced in this page are controllable using the controllers shown below. Please select their type based on intended usage.
Name | Appearance | Max. connectable axis No. | Power source voltage | Control method | Maximum positioning points | ||||||||||||||
---|---|---|---|---|---|---|---|---|---|---|---|---|---|---|---|---|---|---|---|
Positioner | Pulse train | Program | Network *Select | ||||||||||||||||
DV | CC | CIE | PR | CN | ML | ML3 | EC | EP | PRT | SSN | ECM | ||||||||
RCON | ![]() | 16 (ML3,SSN,ECM is 8) | DC24V, single phase AC200V, three phase AC200V | - | - | - | ● | ● | ● | ● | - | - | ● | ● | ● | ● | ● | ● | 128 (Position data unavailable for ML3, SSN and ECM) |
RSEL | ![]() | 8 | - | - | ● | ● | ● | ● | ● | - | - | - | ● | ● | ● | - | - | 36000 | |
SCON-CB/CGB | ![]() | 1 | Single phase AC 100V/200V | ● | ● | - | ● | ● | ● | ● | ● | ● | ● | ● | ● | ● | - | ● | 512 (768 for network specification) |
SSEL-CS | ![]() | 2 | ● | - | ● | ● | ● | - | ● | - | - | - | - | ● | - | - | - | 20000 | |
XSEL-P/Q | ![]() | 6 | Single phase AC200V Three-phase AC200V | - | - | ● | ● | ● | - | ● | - | - | - | - | ● | - | - | - | 20000 |
(Note) Refer to page 8-17 for network abbreviations such as DV and CC.
(Note) 5th and 6th XSEL-P/Q can't be connected.
Oversea specification
(Note) CE is optional.
Important notes on selection
![]() | (1) The horizontal payload indicates the value assuming the rod has a guide attached to it, preventing radial load and moment load to be applied on to it. If it was to be run without a guide, please refer to the relationship between the allowable load at the tip and the running life (→ page 1-293). (2) The payload indicated is the value when the acceleration is 0.3G (0.2G for lead 2.5) in horizontal direction and 0.2G in vertical direction, and the acceleration is the upper limit. (3) The guideline for usable duty varies depending on the operating conditions (transport mass, acceleration/deceleration, etc.). Refer to page 1-282 for further details. (4) The vertical payload indicated is the value when the main body is fixed and the side bracket is operated. Please note that in carrying vertical operation, the main unit can't be operated while the side bracket is fixed. (5) When using vertically, be careful of interference as the rod descends when the power turns off. (6) Safety measures may be required depending on the attachment orientation. Refer to page 1-261 for further details. |
Dimension drawing
ST: Stroke
M.E.: Mechanical end
S.E.: Stroke end
(Note) The rod moves to the M.E. during homing. Please take extra care that the rod may not collide with its surroundings.
(Note) The screwing depth should be equal or less than the indicated dimensions.
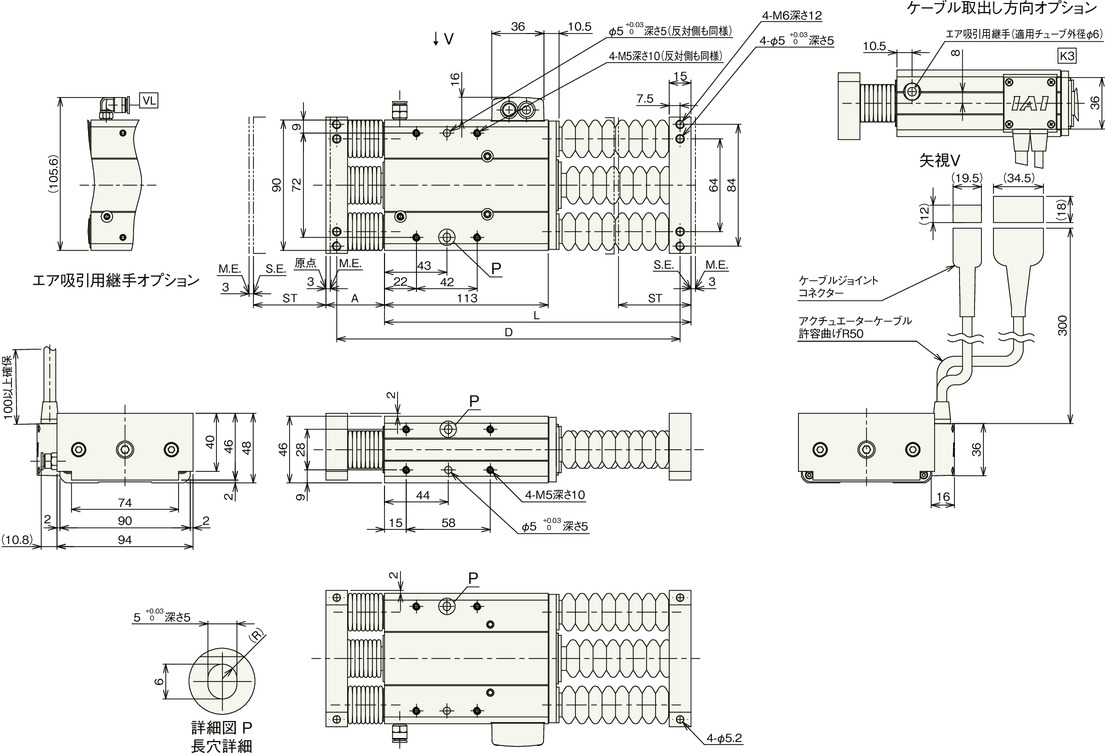
Dimension by stroke length
Stroke | 50 | 75 |
---|---|---|
L | 211.5 | 242.5 |
A | 40.5 | 46.5 |
D | 237 | 274 |
Mass by stroke length
Stroke | 50 | 75 | |
---|---|---|---|
Mass (kg) | Without brake | 2.17 | 2.23 |