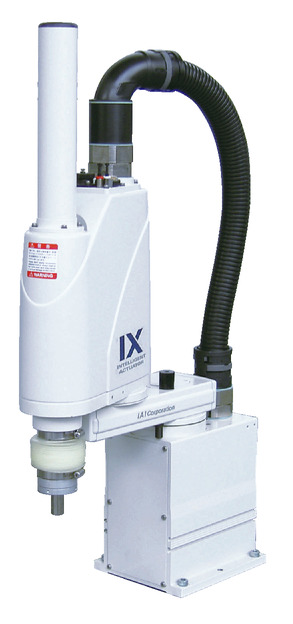
Model specification
Model | Axis Configuration | Arm length (mm) | Motor capacity (W) | Operating range | Positioning repeatability (mm) (Note 1) | Max. PTP operation speed (Note 2) | Standard cycle time (s) (Note 3) | Load Capacity (kg) | Control range of 3rd axis (vertical axis) push force (N) | Allowable load of 4th axis | ||||
---|---|---|---|---|---|---|---|---|---|---|---|---|---|---|
Rated | Maximum | Upper limit (Note 4) | Lower limit (Note 4) | Allowable moment of inertia (kg・m2) (Note 5) | Allowable torque (N·m) | |||||||||
IX-NNW3515H-①-T2-② | 1-Axis | 1st arm | 225 | 200 | ±120 degree | ±0.010 (XY) | 4042mm/s (combined speed) | 0.47 | 1 | 3 | 110.6 | 21.0 | 0.015 | 1.9 |
2-Axis | 2nd arm | 125 | 100 | ±135 degree | ||||||||||
3-Axis | Vertical axis | - | 100 | 150mm | ±0.010 | 1316mm/s | ||||||||
4-Axis | Rotating shaft | - | 50 | ±360 degrees | ±0.005 | 1600 degree/s |
Legend ① Cable length ② Option
Actuator specification
Heading | Contents |
---|---|
Encoder type | Absolute |
User wiring | 15-core AWG26 shielded waterproof connector |
User piping | Air tube (O.D. ø4, I.D. ø2.5) x 3 (Normal working pressure 0.8 MPa) |
Alarm indicator light (Note 6) | 1 small red LED indicator (24V DC supply required) |
Brake release switch (Note 7) | Brake release switch for vertical axis fall prevention (24V DC supply required) |
Ambient temperature/humidity | Temperature 0 - 40℃, humidity 20 - 85% RH or less (no condensation) |
Body weight | 22kg |
Cable length (Note 8) | 5L: 5m (standard) 10L: 10m |
Protective structure (Note 9) | Equivalent to IP65 |
Air purge pressure (Note 10) | 0.3MPa or more (maximum 0.6MPa or less) (clean dry air) |
Adaptive controller
The actuators introduced in this page are controllable using the controllers shown below. Please select their type based on intended usage.
Name | Appearance | Max. connectable axis No. | Power source voltage | Control method | Maximum positioning points | ||||||||||||||
---|---|---|---|---|---|---|---|---|---|---|---|---|---|---|---|---|---|---|---|
Positioner | Pulse train | Program | Network *Select | ||||||||||||||||
DV | CC | CIE | PR | CN | ML | ML3 | EC | EP | PRT | SSN | ECM | ||||||||
XSEL-PX/QX | ![]() | 6 | Three-phase AC200V | - | - | ● | ● | ● | - | ● | - | - | - | - | ● | - | - | - | 20000 |
XSEL-RAX/SAX XSEL-RAXD/SAXD (for IX) | ![]() | 8 | - | - | ● | ● | ● | - | ● | - | - | - | ● | ● | - | - | - | 36666 (depending on type) |
(Note) Refer to page 7-17 for network abbreviation symbols such as DV and CC.
(Note) It can control up to SCARA + 4-axis robot.
(Note) Select XSEL-RAXD / SAXD when connecting two SCARA robots. However, the SCARA robots may not be able to be connected depending on the combination. Refer to page 7-289.
Oversea specification
(Note) CE is optional.
Important notes on selection
![]() | (1) Please refer to page 6-559 for (Note 1) to (Note 11). (2) SCARA robots cannot operate continuously at 100% speed and acceleration. Refer to the technical information on page 1-507 for operating conditions. (3) An adjustment jig is required to perform absolute reset which is needed whenever the encoder absolute data was lost. Refer to page 6-575 for further details. (4) Flange option is available. Refer to page 6-680 for further details. |
Dimension drawing
ST: Stroke
*1 The external force applied to the spacer should be 30N or less in the axial direction and 2N・m or less in the rotational direction. (For each spacer)
*2 The LED operates under a condition where the LED terminal is wired in the user's wiring so that it receives 24V DC while receiving signals from the I/O output of the controller.
(Note) Cable/Piping
・Motor ・Encoder cable 5m/10m
・Brake power supply cable 5m/10m
・User wiring cable 5m/10m
・Air piping (4 pieces) 0.15m
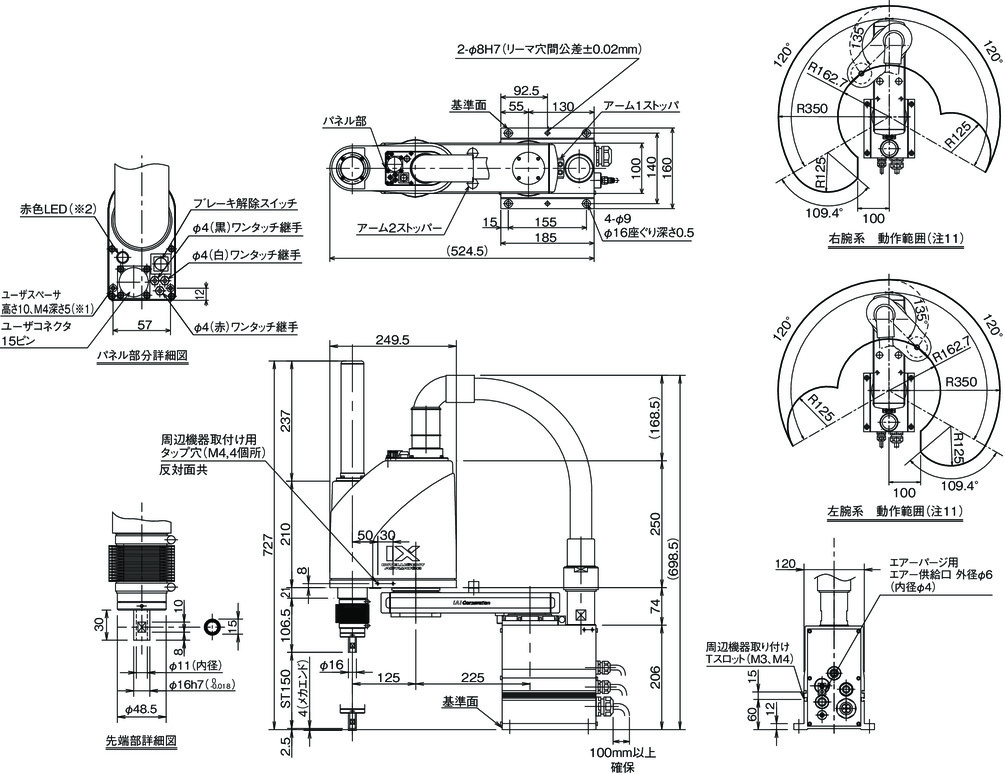